The control arm is one of the key parts of the automobile suspension system. In addition to bearing the weight of the whole body, it will also be subjected to the effect of external dynamic torque and real-time road conditions during driving, which makes the requirements for the manufacturing of the control arm more strict and precise. The optimization of the aluminum alloy control arm shaping technology has always been one of the focuses of continuous research and exploration by people in the industry. The aluminum alloy control arm includes straight arm, curved arm, L-arm and triangular arm. It has the characteristics of variety and complex shape. The forming of the control arm is difficult. It requires multiple forming steps to change a blank with simple shape into a control arm part with complex shape. Its forging process is complex. Feasibility, stability, forming quality, material utilization, forming load, and improving die life are the key points of its forming process.
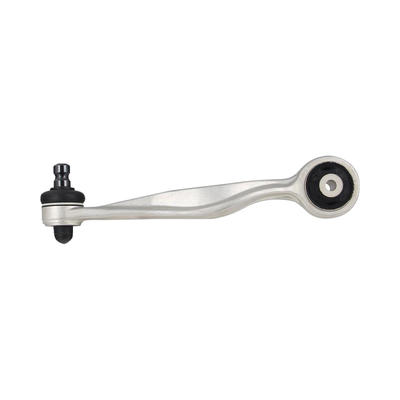
The application of forged aluminum alloy control arm products is a sign of the improvement of automobile manufacturing level, and also a powerful measure to achieve weight reduction and energy saving of vehicles and improve market competitiveness. At present, there are two forging methods for aluminum alloy control arm: one is conventional extrusion rod+forging; The other is special-shaped ingot+forging, which can increase the yield of materials by 15%~20%, and greatly reduce the process. However, European and American systems usually adopt conventional forging methods, which pay more attention to the mechanical properties of forgings. Based on the above analysis, this paper mainly discusses the forging process of the control arm, taking the typical aluminum alloy triangular arm as an example.