With the development of the automobile industry and the increasing pressure on environmental protection, the requirements of automobile factories for lightweight vehicles are increasing. For traditional vehicles, lightweight can significantly reduce fuel consumption; for electric vehicles, lightweight energy can help improve battery performance. cruising range; in addition, the lightweight chassis also improves the vehicle performance in other aspects.
Material selection
At present, the materials for forging aluminum alloy control arms for automobiles are mostly 6061 and 6082 aluminum alloys. The sources of forging blanks include extruded bars, semi-continuously cast bars, and semi-continuously cast special-shaped ingots. Roll forging bending, pre-forging, final forging, heat treatment and other processes; for semi-continuous casting packaging material, it needs to undergo homogenization treatment before cutting; special-shaped ingot refers to the semi-continuous casting method to directly prepare the shape of the ingot and the terminal control arm Near-net-shape aluminum alloy forging billets for automobiles with similar shapes of forged products, ingots are directly forged after slicing. Compared with round bars, the process of special-shaped ingots is greatly shortened, but the casting quality control is more difficult.
Forging billet and die design
For extruded bars, according to the size and volume of the final formed parts, through forging simulation, determine the diameter and cut length of the extruded bars required, and then need to go through heating, roll forging, bending and other processes to make billets; for special-shaped ingots, combined with Casting process and forging simulation, design the required special-shaped ingot shape, and determine the slice thickness of the special-shaped ingot, as shown in the figure below. According to the shape of the final part, the forging die is designed. Sometimes if the part is too complex, it is difficult to form after one forging, or there is a defect after forming, then it is necessary to add a pre-forging to ensure that the forming is defect-free.
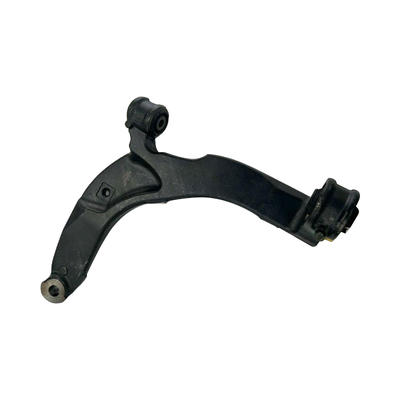
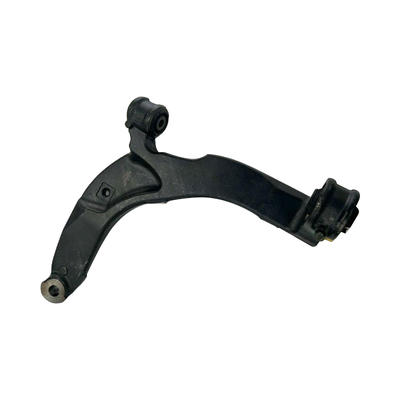
Forging process formulation
The forging process includes the temperature of the blank forging, the temperature of the die, and the heat treatment process after the forging is completed. If the temperature of the blank is too high, it is easy to cause overburning. If the temperature of the blank is too low, the deformation resistance is too large, and the forging filling is difficult. In a suitable range, solid solution and aging treatment should be carried out after forging. The choice of solution temperature and duration is to ensure that the soluble strengthening phase dissolves into the matrix as much as possible without overburning. The aging temperature and duration are different. The selection is based on the premise that the strengthening phase can be uniformly and finely precipitated without coarsening and achieve a better strengthening effect.
Parts organization, performance evaluation
The parts after heat treatment should be tested for low magnification, high magnification, hardness and mechanical properties. The low magnification mainly depends on the abnormal growth of the grains of the parts, which is what we often call the coarse grains. As shown in the figure below, the coarse grains have a negative impact on the mechanical properties of the parts, and the size of the coarse grains or the coarse grain rate should be controlled.