The use of aluminum control arm in automotive applications offers several primary advantages:
Weight Reduction: Aluminum is significantly lighter than traditional steel control arms. By using aluminum, the overall weight of the vehicle can be reduced, leading to improved fuel efficiency, better handling, and increased performance. The lighter weight also contributes to reduced wear on other vehicle components, such as suspension and tires.
Improved Handling and Suspension Performance: Aluminum control arms provide better suspension response and improved handling characteristics. The reduced weight of aluminum arms allows for more precise control of wheel movement, resulting in enhanced stability, reduced body roll, and improved cornering ability. This can lead to a more engaging and enjoyable driving experience.
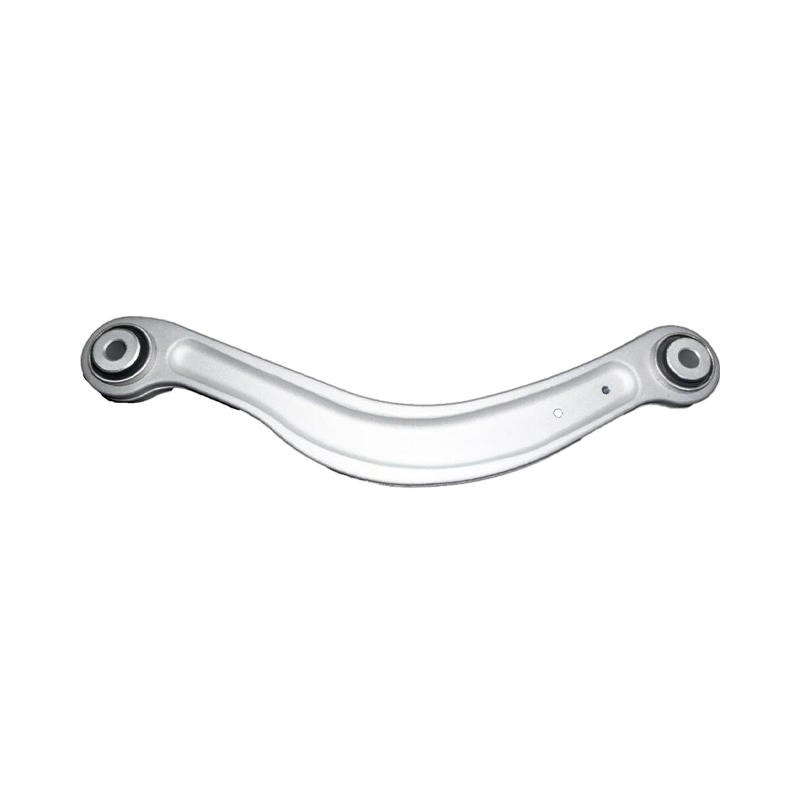
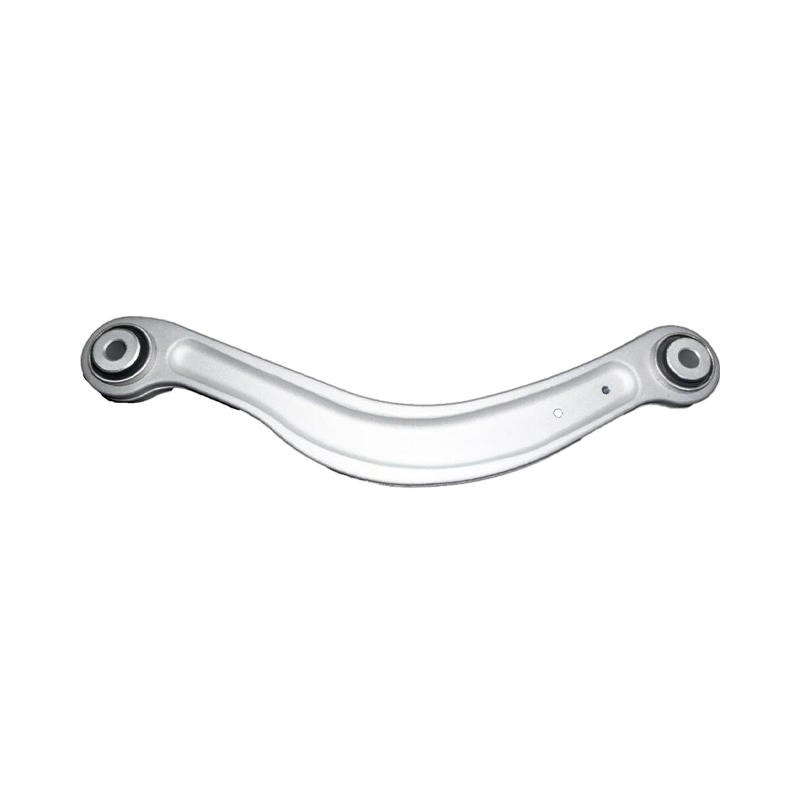
Corrosion Resistance: Aluminum has excellent corrosion resistance properties, making it highly resistant to rust and oxidation. This is particularly advantageous in automotive applications where the control arms are exposed to various environmental conditions, such as moisture, road salt, and chemicals. The corrosion resistance of aluminum control arms helps to extend their lifespan and maintain optimal performance over time.
Design Flexibility: Aluminum is a highly malleable material, allowing for greater design flexibility compared to steel. This flexibility enables automotive engineers to optimize the shape, size, and geometry of control arms to achieve desired performance characteristics. Aluminum control arms can be designed to provide the ideal balance between strength, stiffness, and weight savings, leading to improved suspension tuning and overall vehicle dynamics.
Acoustic Damping: Aluminum control arms have inherent acoustic damping properties. This means they can help reduce noise, vibration, and harshness (NVH) levels within the vehicle's suspension system. By minimizing unwanted vibrations and noise, aluminum control arms contribute to a smoother and quieter ride for occupants.