Aluminum alloy casting refers to the process in which molten metal is injected into the mold under the action of the earth's gravity (gravity casting) or under the action of other external forces (low pressure casting or high pressure casting). The production process is to fill molten aluminum alloy in a liquid state. A process in which the mold cavity is cooled and transformed into a solid state.
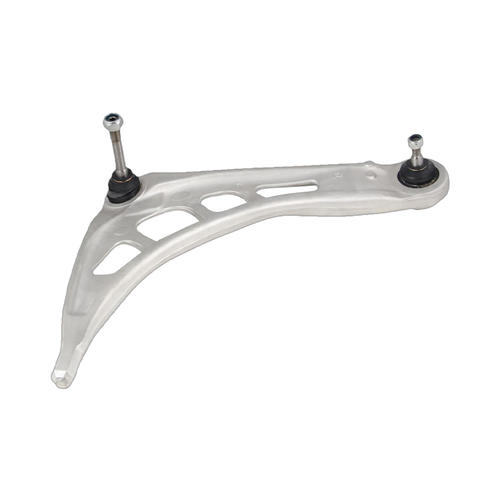
The process of aluminum alloy forging is to heat the billet and undergo plastic deformation, which has the effect of refining grains and continuous fiber cutting. The workpiece obtained by this process has high strength and is easy to anodize. Aluminum forgings are often used for important high-strength parts or require beautiful appearance. The blank manufacturing of the appearance parts.
Aluminum alloy casting has requirements for the aluminum alloy material to be processed. Compared with aluminum forgings, aluminum castings have less advantages. Jiahang aluminum alloy forging indicates that due to the transformation from liquid to solid, defects such as pores and shrinkage are easily generated during the production process. However, casting is suitable for the production of parts with complex shapes, so it is often used for the production of aluminum casting blanks that do not require high mechanical properties.