Jiahang Aluminum Alloy Forging teaches you how to look at the casting performance of aluminum alloy control arms?
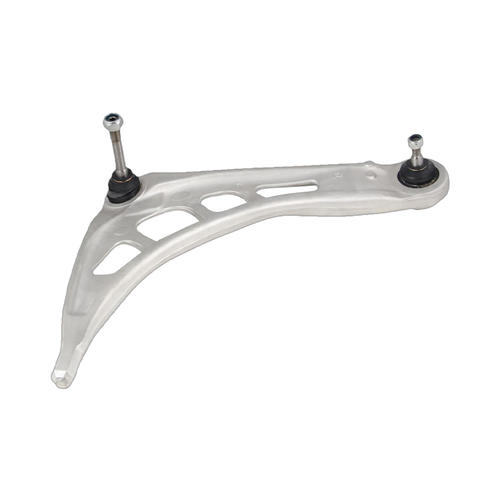
(1) Liquidity.
Flowability refers to the ability of alloy liquid to fill the mold. The degree of fluidity determines whether the alloy can be complex cast. The aluminum crystal system eutectic alloy has the best fluidity.
The flow characteristics of the aluminum alloy control arm are affected by many factors, mainly its composition, temperature, and the presence of solid particles of metal oxides, metal compounds and other contaminants in the alloy liquid, but the basic external factors are the pouring temperature and pouring Pressure (usually called pouring head).
In actual production, after determining the alloy type, in addition to strengthening the smelting (refining and slag removal) process, it is also necessary to improve the mold processability (sand mold permeability, exhaust gas and temperature of the metal mold), and increase the pouring temperature. Ensure the fluidity of the alloy without affecting the quality of the aluminum alloy control arm.
(2) Shrinkage rate.
Shrinkage is one of the main performance indicators of aluminum alloy casting. Jiahang aluminum alloy forging means that in general, the alloy is divided into three stages from pouring to solidification and cooling to room temperature, namely liquid shrinkage, solidification shrinkage and solid state shrinkage. The quality of the aluminum alloy control arm directly affects the shrinkage, shrinkage porosity, stress generation, crack formation and size changes of the alloy material. The shrinkage of the aluminum alloy control arm is usually divided into volume shrinkage and linear shrinkage. In actual production, the linear shrinkage is generally used to measure the degree of shrinkage of the aluminum alloy control arm.
The shrinkage size of the aluminum alloy control arm, usually expressed as a percentage, is called the shrinkage rate.
Contraction in the body
Body shrinkage includes liquid shrinkage and solid state shrinkage.
Jiahang Aluminum Alloy Forging tells everyone that from casting to solidification, macroscopic or microscopic shrinkage of the as-cast alloy will occur at the final solidification. The macroscopic shrinkage caused by this shrinkage is visible to the naked eye, which can be divided into concentrated shrinkage and scattered shrinkage. At the top of the aluminum alloy control arm or at the hot joints with thick and large cross-sections, the apertures of the concentrated shrinkage cavities are large and concentrated; the scattered shrinkage cavities are scattered and small, and most of them are distributed at the axis and hot joints of the aluminum alloy control arm.