Aluminum alloys can be heated before forging with a variety of heating equipment, such as resistance furnaces, gas furnaces, oil furnaces, induction heating installations, fluid particle furnaces, etc. In China, resistance furnaces are generally used for heating. In this case, it is better to have a forced furnace gas circulating installation in the furnace to make the furnace temperature average. When using a gas furnace or an oil furnace, low-sulfur fuel must be used, and the flame in the furnace is not allowed to directly radiate the surface of the billet. Foreign countries think that the muffle furnace is the best for aluminum alloy forging heating, and the gas semi-closed furnace has been widely used. When the aluminum alloy forging process is highly automated, the commonly used heating methods include induction heating, resistance heating and fluid particle heating.
The forging temperature range of aluminum alloy is narrow, and it is easy to overheat and burn, so it is necessary to accurately measure and control the temperature, and the furnace temperature deviation is preferably within the range of ±5 °C.
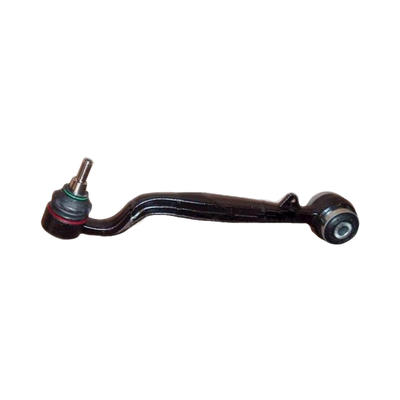
Aluminum alloy has good thermal conductivity, so blanks of any thickness can be directly heated in a high-temperature furnace without preheating, but the heating time is longer than that of ordinary carbon steel. This is because the internal strengthening phase must be fully dissolved when the aluminum alloy is heated. In order to make the alloy structure uniform and plasticity progress. The heating time of the aluminum alloy billet is calculated as 1.5 to 2 minutes per millimeter of diameter or thickness. The dissolution process of the strengthening phase is related to the size, shape, dispersion characteristics and its own properties of the strengthening phase. The coarser the structure, the slower the dissolution. Therefore, the upper limit of the heating time should be taken for ingots, large forgings and rough bars (above φ100mm). For billets with high alloying element content, the heating time is longer. For example, the heating time of LC4 alloy should be longer than that of LD2 alloy. Under normal circumstances, the heating time of the aluminum alloy is enough for 1-2h. If it encounters a unavoidable extension, the heating time can exceed 4-6h. If it is longer, it is recommended to take the metal out of the furnace to prevent overheating and absorption. hydrogen.
Sichuan Hongyi Intelligent Machinery Co., Ltd. is professional China Automotive Aluminum Steering Control Arms Manufacturers and Automotive Aluminum Steering Control Arms Wholesale. Hongyi Intelligent Machinery is strong in technology and R&D, is the OE supplier of FAW Group Corporation and is recognized as a "high-tech enterprise" by the government. The company integrates a precision forging plant and a mechanical processing plant, based on high-grade and high-end markets, with an annual output value of up to 80 million yuan. For any customer orders for wholesale Automotive Aluminum Steering Control Arms, we will complete them on time, quality and quantity.
Sichuan Hongyi Intelligent Machinery Co., Ltd. is professional China Automotive Aluminum Steering Control Arms Manufacturers and Automotive Aluminum Steering Control Arms Wholesale. Hongyi Intelligent Machinery is strong in technology and R&D, is the OE supplier of FAW Group Corporation and is recognized as a "high-tech enterprise" by the government. The company integrates a precision forging plant and a mechanical processing plant, based on high-grade and high-end markets, with an annual output value of up to 80 million yuan. For any customer orders for wholesale Automotive Aluminum Steering Control Arms, we will complete them on time, quality and quantity.