The forging stress of aluminum alloy forging includes thermal stress, transformation stress and compression stress. The reasons for various stresses are not the same.
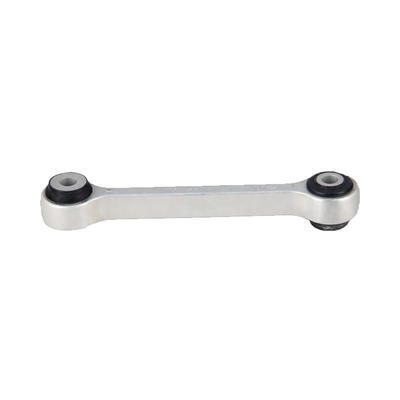
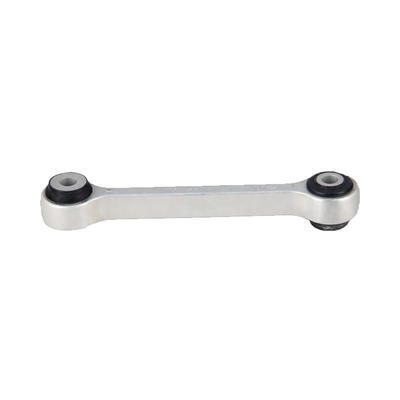
(1) Thermal stress. Thermal stress is caused by the uneven thickness of the cross-section at the intersection of the casting and the difference in cooling, etc. Compressive stress builds up at thin walls, resulting in residual stress in the casting.
(2) Phase transformation stress. The phase transformation stress is due to the phase transformation of some cast aluminum alloys during the cooling process after agglomeration, resulting in a change in volume and size. Aluminum alloy forging means that the main reason is that the wall thickness of the aluminum casting is uneven, and the phase transformation occurs in different parts at different times.
(3) Compressive stress. When the aluminum casting is compressed, it is blocked by the mold and core and produces tensile stress. This stress is temporary, and the aluminum casting will actively dissipate out of the box. However, if the unpacking time is not right, it will often cause hot cracks, especially the aluminum alloy cast in the metal mold is often prone to hot cracks under the action of this stress.
Aluminum alloy forging means that the residual stress in the cast aluminum alloy parts reduces the mechanical properties of the alloy and affects the machining accuracy of the casting. Residual stress in aluminum castings can be eliminated by annealing treatment. Due to the good thermal conductivity of the alloy, there is no phase change during the cooling process. As long as the casting layout is reasonable, the residual stress of the aluminum casting is generally small.