Aluminum is forged at a much lower temperature than any other common metal because of its low melting point. Aluminum's low density results in its low ability to retain heat. Therefore, hot working is necessary to avoid rapid cooling of the workpiece. The die temperature can often be equal to or close to the billet temperature, a condition commonly referred to as isothermal forging. Fortunately, most die steels are not tempered when used in the isothermal forging process of aluminum. Typical forging temperature range is 775-875°F.
For most forging applications, the billet material undergoes some deformation treatment (cogging, rolling or extrusion) to destroy the cast grain structure. For aluminum, continuous casting billets are more common. The slab can be homogenized when a more consistent microstructure is required. There are some pores in the billet that must be "healed" by forging. Of course, extruded and forged billets are also used. Billets are usually sawn. Due to the high ductility and low melting temperature of aluminum, abrasive saws are not used.
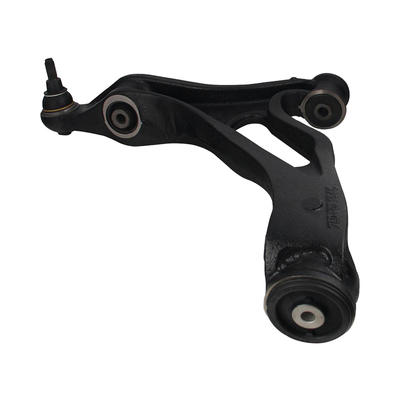
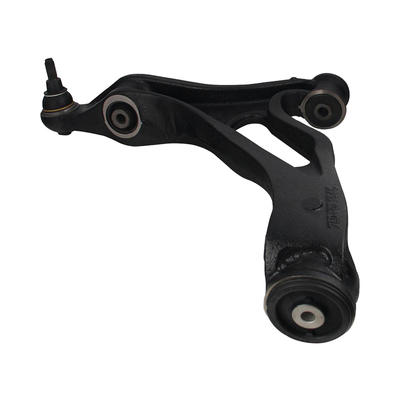
Most forging billets are heated in gas or electric furnaces. Aluminum has a significantly lower melting point than other common metals, so convection is the dominant heat transfer method due to the relatively low forging temperatures required. Radiation predominates in metals forged above 1500°F. Since aluminum is not ferromagnetic, induction heating is impractical.
Aluminum alloys are usually forged on hydraulic presses because of their high strain rate sensitivity. Using hammers and mechanical presses is the exception rather than the rule. Ram speeds are generally slower, typically 1 inch/sec or less. Hot molds, including isothermal molds, are common. In most cases, the tool temperature is within 250°F of the workpiece temperature. For net shape/precision forgings, isothermal dies and low strain rates are the norm.
Hammer forging of aluminum alloys requires care. Due to the high deformation rate of the hammer, one may experience hot brittleness in the workpiece. Lubrication has evolved over the past 25 years, with leaded lubricants being phased out in the 1980s. Currently, oil-based lubricants are being replaced by water-based and synthetic lubricants. Lubrication is a critical aspect when forging aluminum, as the metal has a strong tendency to wear (ie, pieces of aluminum workpiece stick to the die).
Immediately after forging, high-volume parts (automobiles) are heat treated on an automated production line. Disposable parts, such as some used in the aerospace industry, are air-cooled. Post-forging cold working is done by stamping to Steering control arm control dimensional and residual stresses in critical applications.