As the force transmission and guiding element of the automobile system, the control arm transmits various forces acting on the wheels to the car body, and at the same time ensures that the wheels move according to a certain trajectory. With the development of manufacturing technology and material technology, automobile control arms have gradually replaced traditional casting by forging. The complete process flow of the aluminum alloy suspension control arm is generally: blanking-rounding-intermediate frequency induction heating-roll forging-flattening and bending-secondary heating-die forging-hot trimming-solution-aging, but the existing The production process is easy to cause defects such as folding and shrinkage of the processed control arm. The blank needs to be heated many times, and the processing efficiency is low.
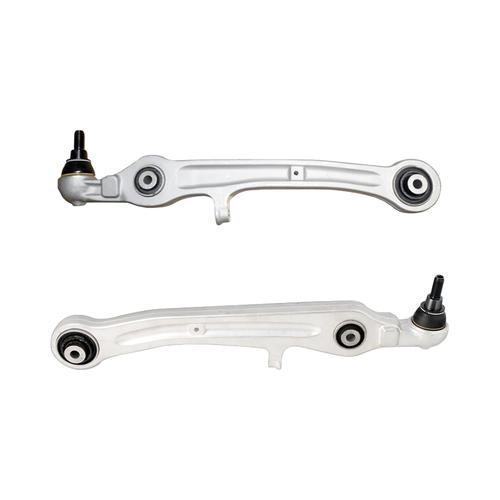
Technical realization elements:
The technical problem to be solved by the present invention is to provide a forging method of an automotive aluminum alloy control arm. The control arm forged by the method is well formed without defects such as folding and shrinkage.
The solution to the technical problem of the present invention is:
A forging method of automotive aluminum alloy control arm is characterized in that it comprises the following steps:
(a) Using extruded round bars as blanks;
(b) Heat the sawn blanks, and heat the blanks to between 500°C and 520°C;
(c), the first pass forging: using the first pass forging die, the first pass forging die includes the first upper roller forging die and the first lower roller forging die arranged up and down, the heated The blank is fed into the first pass forging die and positioned, the first upper forging die and the first lower forging die rotate and forge a section of the blank. The section where the blank is forged is from a circular cross-section to an ellipse. The cross-section is deformed to obtain the first pass forgings;
(d), the second pass forging: using the second pass forging die, the second pass forging die includes the second upper roller forging die and the second lower roller forging die arranged up and down, the first pass The secondary roller forging is rotated 90° around its own axis and then sent to the second roller forging die and positioned. The second upper roller forging die and the second lower roller forging die are elliptical in cross section to the first roller forging die. Roll forging is performed on a section of the first pass, and the section of the first pass forged by roll forging is deformed from an elliptical section to a flat section, so as to obtain the second pass forging;
(e) Flattening and bending: a bending die is used. The bending die includes a bending lower die and a bending upper die set up and down, and the second pass roll forging is put into the bending die. The second pass roller forging is placed on the lower bending die, and the upper bending die moves downward. The upper surface of the second pass roller forging is compressed and the lower surface is stretched. The second pass roller forging is finally subjected to local compression. Form a curved workpiece;
(f) Final forging forming: using a final forging die, the final forging die includes a final forging upper die and a final forging lower die set up and down, the bent workpiece is fed into the final forging die, and the bent workpiece is put into the final forging The lower die is positioned well, and the upper die for the final forging moves downwards, and the bent workpiece undergoes plastic deformation, and finally the control arm is obtained.